The Influence of Plastic Mold Quality on Injection Molding Production
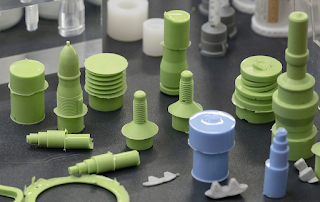
The purpose of mold design and manufacturing is for the mass production of injection parts with high efficiency and high quality, to produce high-quality plastic parts , the first mold is good, a good set of plastic molds is not just a good look, want to do a set of high-quality, high level, high precision plastic molds, from the following aspects. 1. The smoothness of the injection mold surface The polishing of the mold surface is very important, which is one of the most important links to determine the success or failure of mold manufacturing. The surface of the mold is not smooth enough, its surface is uneven, and the surface of the plastic parts injected will have skin lines and sand grains. Generally, the polishing surface into a mirror is good, in addition to the choice of mold steel, grinding personnel, time, technology will have an impact on the polishing mirror effect, requiring a professional mold polishing master, experience to be particularly rich in order to accurately ...